Digital fabrication is a revolutionary technology that leverages computer-controlled processes to create physical objects from digital designs. This approach has dramatically transformed various industries, including manufacturing, architecture, and consumer goods, by introducing new levels of precision, customization, and efficiency. This article delves into the key aspects of digital fabrication, including its principles, technologies, applications, benefits, challenges, and future prospects.
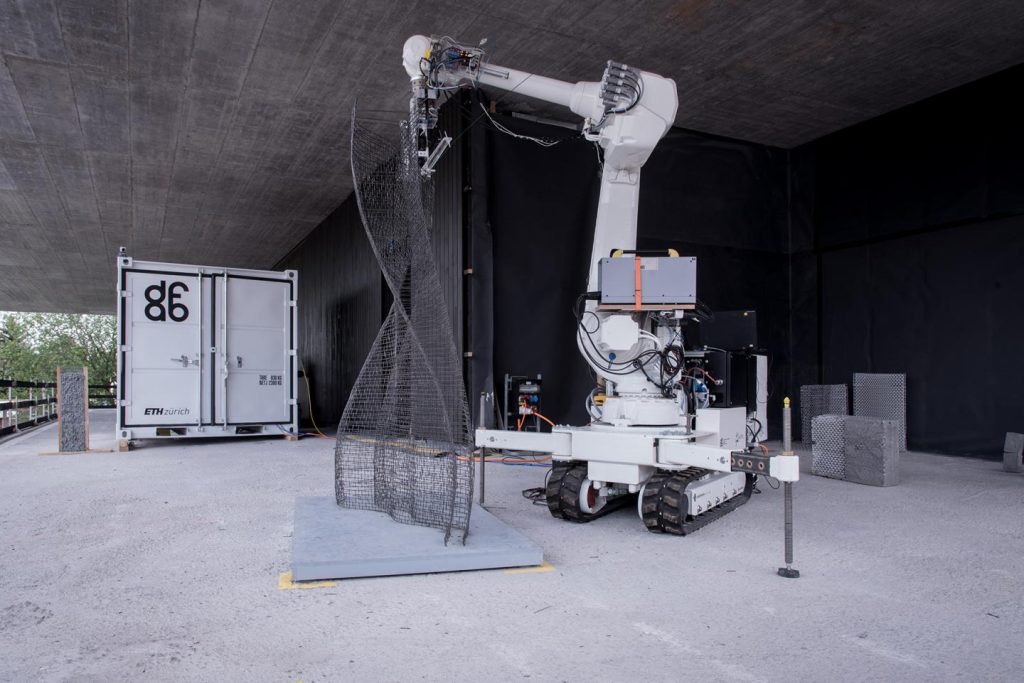
Understanding Digital Fabrication
Digital fabrication refers to the use of digital tools and technologies to design and produce physical objects. Unlike traditional manufacturing methods, which often involve multiple stages and manual processes, digital fabrication relies on computer-driven processes to create objects directly from digital models. This approach simplifies production, reduces waste, and allows for greater customization and flexibility.
1. Key Principles:
- Digital Design: Digital fabrication starts with a digital design or model, which is created using computer-aided design (CAD) software. The design is then converted into machine-readable instructions.
- Automated Production: Computer-controlled machines execute the design instructions to fabricate the object. This can involve processes like cutting, milling, 3D printing, and laser engraving.
- Iterative Prototyping: Digital fabrication enables rapid prototyping, allowing designers and engineers to quickly iterate and test their designs before moving to production.
Technologies in Digital Fabrication
Digital fabrication encompasses various technologies and techniques, each suited to different types of materials and applications. Some of the most prominent technologies include:
1. 3D Printing (Additive Manufacturing):
- Definition: 3D printing builds objects layer by layer from a digital model. It can use materials like plastics, metals, and ceramics.
- Applications: Used in prototyping, custom manufacturing, medical implants, and architectural models.
2. Computer Numerical Control (CNC) Machining:
- Definition: CNC machining involves using computer-controlled tools to cut, mill, and shape materials. CNC machines can handle a variety of materials, including metals, plastics, and wood.
- Applications: Common in manufacturing parts, tooling, and complex geometries in industries like aerospace and automotive.
3. Laser Cutting and Engraving:
- Definition: Laser cutting uses a high-powered laser to cut or engrave materials based on a digital design. It offers high precision and clean edges.
- Applications: Used for creating intricate designs in materials like acrylic, wood, and metal, often in signage and art.
4. Inkjet Printing:
- Definition: Inkjet printing deposits layers of ink to create images or patterns on various surfaces, including textiles and ceramics.
- Applications: Employed in creating custom textiles, ceramics, and packaging materials.
5. Digital Weaving and Knitting:
- Definition: Digital weaving and knitting use computerized looms and machines to create complex textile patterns and structures.
- Applications: Utilized in fashion, upholstery, and technical textiles.
Applications of Digital Fabrication
Digital fabrication has found applications across various fields, revolutionizing traditional practices and enabling new possibilities.
1. Manufacturing and Industry:
- Customization: Digital fabrication allows for mass customization, enabling the production of personalized products without significant additional costs.
- Rapid Prototyping: Designers and engineers can quickly create and test prototypes, speeding up the development process and reducing time-to-market.
2. Architecture and Construction:
- Complex Geometries: Digital fabrication techniques enable the construction of complex architectural forms that would be difficult or impossible with traditional methods.
- Parametric Design: Architects use parametric design tools to create dynamic structures that can be easily modified and optimized using digital fabrication.
3. Healthcare and Medical Devices:
- Custom Implants and Prosthetics: 3D printing is used to create custom implants and prosthetics tailored to individual patients’ needs.
- Surgical Planning: Digital models and simulations assist in planning complex surgeries and designing surgical instruments.
4. Consumer Goods and Fashion:
- Personalized Products: Consumers can customize products such as jewelry, footwear, and accessories using digital fabrication techniques.
- Innovative Designs: Fashion designers use digital fabrication to create unique garments and accessories with intricate patterns and textures.
5. Education and Research:
- Hands-On Learning: Digital fabrication tools provide students with hands-on experience in design, engineering, and manufacturing.
- Innovation and Experimentation: Researchers use digital fabrication to explore new materials and techniques, pushing the boundaries of what is possible.
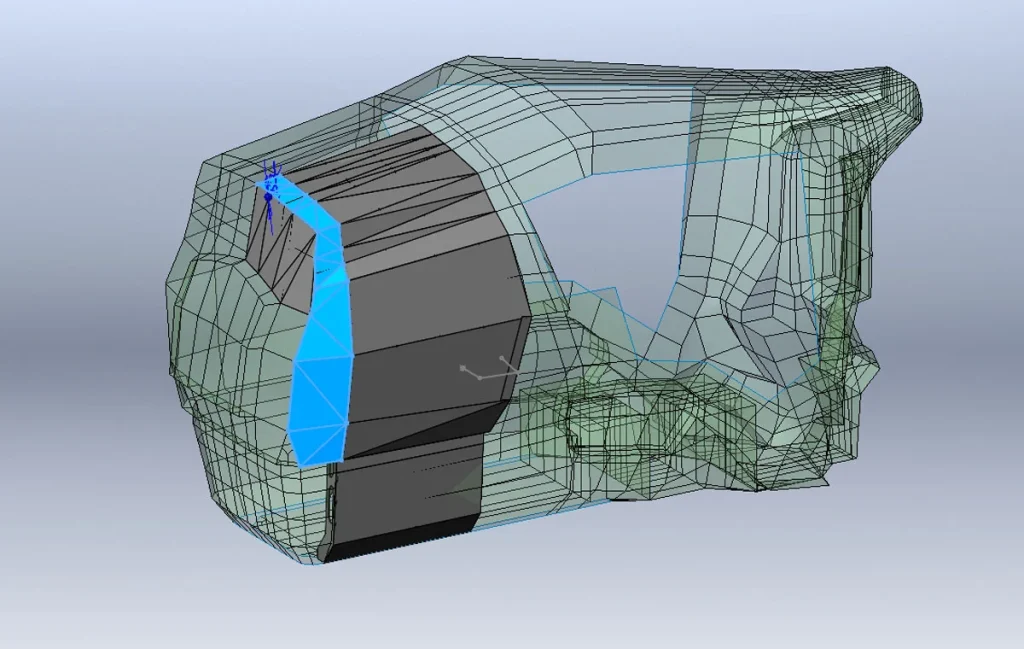
Benefits of Digital Fabrication
1. Precision and Accuracy:
- Enhanced Quality: Digital fabrication technologies offer high precision and accuracy, resulting in well-crafted and detailed products.
- Reduced Errors: Automated processes reduce human error and variability, ensuring consistent quality.
2. Efficiency and Cost Savings:
- Reduced Waste: Digital fabrication minimizes material waste by producing only the required amount of material.
- Cost-Effective Production: With the ability to produce custom parts and products on demand, digital fabrication reduces the need for large inventories and costly tooling.
3. Customization and Flexibility:
- Personalization: Digital fabrication allows for easy customization of products to meet individual preferences and specifications.
- Design Flexibility: Designers can experiment with complex geometries and materials without the constraints of traditional manufacturing methods.
4. Rapid Prototyping and Innovation:
- Faster Development: Rapid prototyping enables quick iterations and testing, accelerating the development cycle for new products and innovations.
- Creative Exploration: Designers and engineers can explore new ideas and concepts without the limitations of traditional production techniques.
Challenges and Considerations
1. Material Limitations:
- Material Compatibility: Digital fabrication technologies may have limitations in the types of materials they can work with, affecting the range of applications.
- Material Properties: The properties of fabricated materials may differ from those produced using traditional methods, requiring careful consideration.
2. Technical Expertise:
- Skill Requirements: Effective use of digital fabrication technologies requires specialized knowledge and skills in design, programming, and operation.
- Training and Education: Ensuring that individuals and teams are trained in digital fabrication techniques is essential for successful implementation.
3. Cost of Equipment:
- Initial Investment: The cost of acquiring and maintaining digital fabrication equipment can be high, especially for advanced technologies.
- Accessibility: Smaller businesses and individuals may face challenges in accessing and affording digital fabrication tools.
4. Intellectual Property:
- Design Protection: The ease of digital replication raises concerns about protecting intellectual property and preventing unauthorized copying of designs.
- Patent Issues: Navigating patent and copyright issues related to digital designs and fabrication processes can be complex.
Future Trends and Developments
1. Advancements in Materials:
- New Materials: Research into new materials and composites will expand the possibilities of digital fabrication, enabling the creation of more diverse and advanced products.
- Sustainable Materials: The development of eco-friendly and sustainable materials will address environmental concerns and promote responsible manufacturing practices.
2. Integration with Other Technologies:
- Internet of Things (IoT): Integration with IoT technologies will enable smart and connected fabrication systems that can monitor and optimize production processes.
- Artificial Intelligence (AI): AI and machine learning will enhance design and manufacturing processes, enabling more intelligent and adaptive fabrication systems.
3. Expansion of Applications:
- Medical Innovations: Continued advancements in digital fabrication will lead to new innovations in medical devices, implants, and personalized healthcare solutions.
- Architectural Innovation: Digital fabrication will support the creation of more complex and innovative architectural designs, pushing the boundaries of modern construction.
4. Accessibility and Democratization:
- Affordable Tools: The development of more affordable and accessible digital fabrication tools will democratize manufacturing and design, enabling broader participation and innovation.
- Educational Resources: Increased availability of educational resources and training will support the widespread adoption and application of digital fabrication technologies.
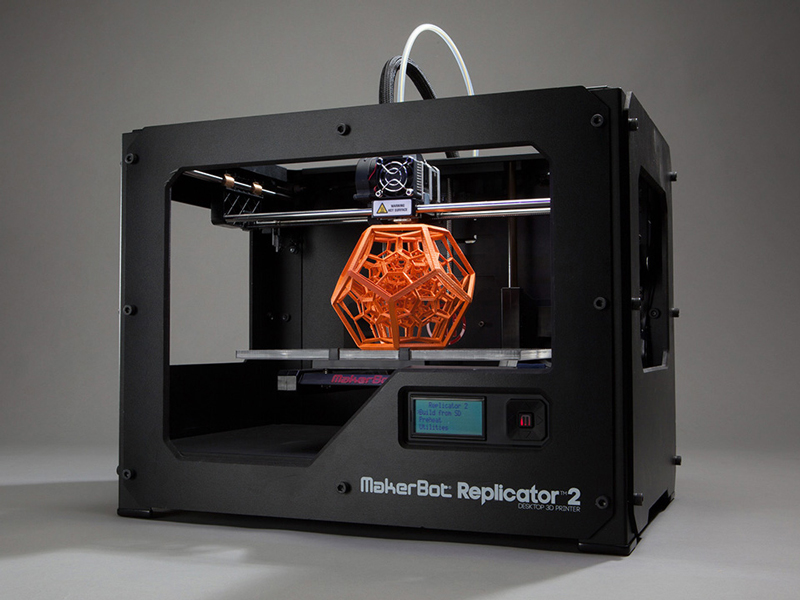
Conclusion
Digital fabrication represents a transformative shift in production and design, offering new levels of precision, customization, and efficiency. By leveraging computer-controlled processes and technologies, digital fabrication enables rapid prototyping, innovative designs, and personalized products. While challenges related to materials, expertise, and costs remain, the future of digital fabrication holds exciting possibilities for advancing technology, enhancing creativity, and improving various industries. As digital fabrication continues to evolve, it will undoubtedly play a pivotal role in shaping the future of manufacturing and design.